OUR MINES & Plants
Al Masane Copper Zinc Mine (Underground)
This mine is located in Najran, in the southwest of the Kingdom, specifically in Thar Governorate, at an altitude of more than 1,600 above sea level. The establishment of industrial facilities in the mine began in 2008 and commercial production began in 2012.
Ore Processing at Al Masane Plant
The company applies several stages to recover precious and semi-precious metals of crushed ore, starting with units where the crushed ore is separated from the jaw crusher and stored in a designated place on the surface, to be then transported to the semi-automated mill and crushed into millimetric particles, which are transferred to the ball mill, operates using steel balls for crushing and grinding, which turns the rocks into magmatic sizes, and is treated with special chemicals to adjust pH levels, and stimulate the formation of bubbles. These processed ore materials are then transferred to flotation cells which remove talc, copper and zinc, respectively. Each flotation cell consists of dimensional filter units (coarse, less coarse, fine, and precise) to gradually clean, purify and separate the minerals until our precious metals are produced using the filtration stage and then filtered to be purified, precipitated and forming a mixture of precious metals, followed by smelting gold and silver and forming their alloys .
Underground Mining
After reaching the two main mine bodies (Saadah and Al Houra) at a depth of 291 meters, according to several sub-levels separated vertically by 20 to 30 meters, which are linked by a series of spiral slopes; multiple materials lenses are traced and tunnels developed at each level to reach a height of 4.5 meters and a width of 4.5 meters, which are formed according to special drilling and blasting operations. Economically viable ore rocks are loaded and transported via a fleet of special loading vehicles, including advanced heavy loaders and trucks. The ore is transported for storage above ground. The uneconomical rocks are used to backfill the places where production has been exhausted. The direction of the tunnel extension is also precisely controlled in the company’s geology department. The basic services for mining operations are provided, including electricity, water, ventilation, communication systems and sewage pumping systems, and distributed throughout the mine.
Processing and Production:
Al Masane Plant for Processing includes copper and zinc as a main product, where 800,000 tons were processed from the beginning by the flotation method. The factory’s production capacity of copper concentrates reached 21,971 tons, zinc concentrates 42,398 tons. Gold and silver are by-products. The company produced 7,197 ounces of gold and 105,649 ounces of silver until the end of 2021 AD. Products are transported and exported through the port of Jazan.
Mining licenses:
1. Al-Masanea license with an area of 42.07 km²
Al Masane Process Plant diagram
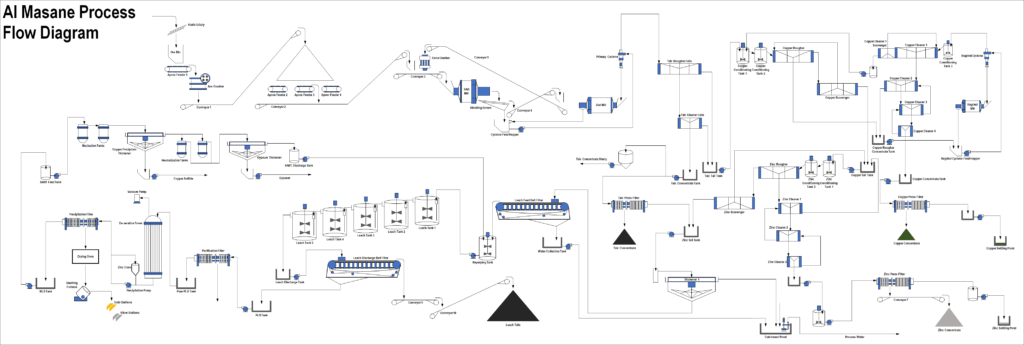
Al Masane Plant Process Description
The Al Masane Plant utilizes several unit operations to recover base and precious metals from a blend of Saadah, Al Houra and Moyeath ore sources: namely Crushing, Grinding, Flotation, Dewatering, using Cyanidation, Merrill-Crowe and SART (Sulphidization, Acidification, Recycling and Thickening). The final tailings material is dry-stacked in a Tailings Storage Facility (TSF).
Crushed ore is stockpiled and conveyed to a Semi-Autogenous (SAG) Mill for primary grinding. A Ball Mill completes the two-stage grinding process to reduce ore particle size for the Flotation process.
The Flotation process starts with removal of talc by flotation at low pH to ensure minimal sulphide mineral losses. Copper and zinc ore is processed through rougher, scavenger and cleaner stages to produce marketable concentrate grades at budget recoveries.
The flotation concentrates are filtered to attain 8-10% moisture content for storage, transport and shipment. Flotation tailings is dewatered to recover process water, while thickened slurry gravitates to belt filters for further removal of process water in preparation for leaching of gold and silver through cyanidation process.
The belt filter cake is repulped using SART solution before processed in a battery of leach tanks. Gold, silver and copper -zinc metals are dissolved using a low cyanide concentration solution along with oxygen from injected compressed air. The leach tailings undergo solid-liquid separation where the Pregnant Leach Solution (PLS) is stored in a tank for Merrill-Crowe process, while the solids are conveyed to a stockpile before transportation to the TSF.
The Merrill-Crowe process recovers precious and base metals by precipitation with zinc dust. The precipitates are continuously pumped to press filters where the filtrate is stored in the Barren Leach Solution (BLS) Tank before pumping to the next stage. The precipitates are harvested and smelted into gold and silver bullions.
The SART process receives the BLS and precipitates heavy metals to free the cyanide. The process includes a neutralization step to ensure cyanide remains in solution form before pumping to the repulping stage. The precipitate is rich in copper which is pumped to the flotation circuit to combine with final copper concentrates.
Guyan Gold Mine: Open Mine (Above Ground)
This mine is located in Najran region in the southwest of KSA, 17 km from Al Masane mine. Processing operations for mining began in 2019 and the factory was prepared in late 2020. The Factory was commissioned in early 2021 AD, which was designed and built to produce up to 35,000 thousand ounces annually.
The first gold smelting from Guyan Gold Mine was done in January 2021. From this point, the journey of Guyan Gold Mine began in the production of gold and silver ingots.
Ore Processing at Guyan Plant
The plant recovers precious metals from gold and silver using “CIP” and gravity concentration. The operations begin with liberating the precious metals from the ore through closed crushing and grinding circuits, making sure that the appropriate size of the powder is reached, then the powder sizes are classified into fine and coarse particles. Heavy precious metals are recovered in the concentration circuit by gravity due to their weight and volume. Light precious metals are recovered in CIP. From “CIP” and gravity concentration, a carrier solution for precious metals is produced to be passed to the electro-extraction process. Precious metals are collected from the cells of the electrowinning process to move to the smelting process and form gold and silver alloys. Bullion is exported to suppliers who re-refine it. Guyan factory uses filtration to reduce water consumption and reuse it in operations, believing in the principle of AMAK to achieve optimal water rationalization and compliance with the achievement of Vision 2030.
GUYAN Plant Process Description
The GUYAN Plant utilizes several unit operations to recover precious metal particularly gold from an orogenic type of gold ore sources and classified in to two types, oxide and sulfide: namely Crushing, Grinding, Gravity Concentrator, Cyanidation by Leaching, Carbon Absorption, Elution and Stripping, Electrowinning and Smelting, Dewatering, the final tailings material is dry-stacked in a Tailings Storage Facility (TSF).
Crushed ore is stockpiled and conveyed to a Primary Ball Mill for primary grinding. A Secondary Ball Mill completes the two-stage grinding process to reduce ore particle size for the Gravity concentration and Leaching process.
The Gravity concentration process starts will recover the gold nuggets or native gold and the finer gold ore material will be process in a cyanidation by Leaching it to produce pregnant solution along with oxygen from injected compressed air. This pregnant solution will go to a series of carbon absorption tanks, where the activated carbon will absorb the gold solution.
The carbon loaded or bearing gold carbon will under go for the Elution and stripping process. This where the gold will be strip from the carbon via eluate solution and this solution will pass by an Electrowinning cell to recover and produced precipitates or gold cakes. The precipitates are harvested and smelted into gold bullions.
The final carbon absorption tank tailings will undergo in a solid-liquid separation. Slurry solution will be separated first via thickening process where the water will be recycled and the suspended solids will be treated by flocculants to make it settle and will undergo to filtering process where the filtrate water will go back to the system, while the solids are filtered to a stockpile before transportation to the TSF.
Processing and Production:
The gold is processed in the advanced processing plant, which is one of the most modern processing methods, where the ore goes through stages, starting with crushing and grinding, then moving to the classification stage, and then filtration through the CIP and gravity concentration circuits, ending with smelting to produce gold and silver alloys.
The production capacity of the plant is about 400,000 tons per year.
Production amounted to 17,706 ounces of gold.
Mining licenses:
1.Guyan license with an area of 10,057 km²
Guyan Process flow diagram
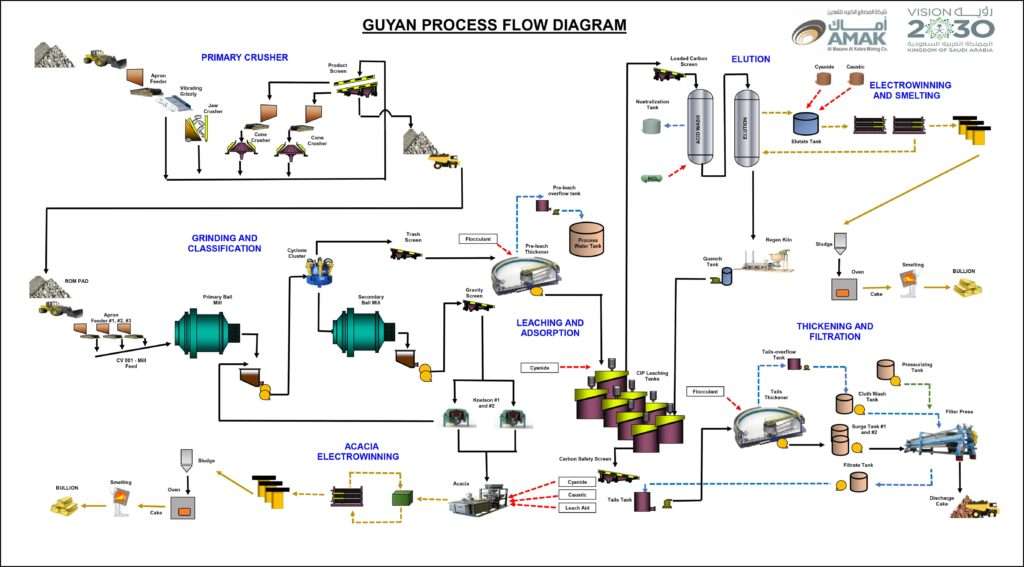
Expansion of the Al Masane Al Kobra Mining Mine Project " Moyeath orebody " (Underground)
Moyeath orebody is located in Najran region in the southwest of the Kingdom. It is an expansion of the Al- Masane mine, as it contains high levels of zinc, silver, and large quantities of copper and gold compared to Saadha and Al-Houra Orebodies.
AMAK has conducted studies and testing on the metals in the mine in the year 2020 AD. Studies and tests have proven the availability of ore to a large extent.
Processing and Production:
During 2021, AMAK decided to design a new processing plant using the latest technology, which is expected to have a production capacity of 400,000 tons per year, which will lead to an increase in the production capacity of base metals by 50%, with a total of 1.2 million tons per year.
According to the expected timetable for the start of operation of the new processing plant in 2023, the total production of AMAK will increase by a large percentage, up to 80% of zinc and 50% of copper.
Work is underway to develop the infrastructure for resources and underground exploration operations to enhance the process of producing high-quality ore throughout the operation of the processing plant, thus prolonging the life cycle of the mine for more than 10 years.
MINING
GOLD
We produce 25,000 Oz of gold from different mines – Underground Al Masane Mine and Guyan open pit that allow us to be a manufacturer of raw gold. Gold is one of the most desired & luxury metals
and is mainly used in making jewellery. It is also utilized in electronic devices.
MINING
SILVER
We produce 105,600 Oz of silver it used in various industrial sectors because of its versatile nature. It is used in the electronics industry and has seen a huge growth in demand for use in solar panels manufacture. Silver is also used in alloys, coatings, medicine and many other applications.
MINING
COPPER
We produce over 22,000 tons of high-quality copper concentrate annually. Copper is used in a variety of electronic equipment due to its conducting capabilities. Demand for copper is expected to increase as electric vehicles manufacturing takes off.
MINING
ZINC
We produce over 42,000 tons of high-quality Zinc concentrate annually. Zinc, due to its anti-corrosion properties, is widely used for the coating of iron and steel. This metal is also valuable for the production of brass. It is to be noted that zinc is also used in medicine as a health supplement.